Ingrid de Keijser
La inteligencia se asocia con la capacidad de comprender. En el caso de las fábricas, este acto se logra interconectando información para resolver, predecir y evitar problemas de manera rápida y flexible.
Las fábricas inteligentes son el resultado final de la aplicación e integración de tecnologías para una mayor automatización y digitalización de la manufactura. El objetivo es conectar al mundo físico con el mundo virtual para iterar, aprender y actuar, optimizando recursos y tiempo.
Las ventajas de las implementaciones de fábricas inteligentes son claras: mejora en gestión de inventarios, monitoreo selectivo pero adecuado de la calidad, disminución de tiempos muertos por fallas imprevistas, menos mantenimientos correctivos y planeados.
A través de las fábricas inteligentes es posible, entonces, contar con producciones más versátiles, eficientes y autónomas, permitiendo a las personas enfocar su atención en identificar y analizar espacios de mejora y dedicar menos tiempo a la parte operativa y repetitiva.
Sin embargo, para que un sistema esté interconectado de manera completa, es imprescindible pasar por varias etapas y sobreponerse a retos de distintas índoles:
- Sentar los objetivos
Aunque pareciera obvio, en muchos casos no queda claro el porqué de las implementaciones de una fábrica inteligente. Suena bien contar con una fábrica inteligente, pero lo principal es saber qué se quiere saber y por qué. Para ello, resulta esencial determinar objetivos de monitoreo para poder seleccionar las variables, frecuencias e interconexiones necesarias de los dispositivos y condiciones de producción.
Primero determinar el para qué, después qué y posteriormente cómo hacerlo.
Con la tecnología actual es posible dar seguimiento a un sinfín de procesos productivos, que van desde aprendizajes de las máquinas que relacionan y predicen comportamientos de distintos datos -tales como la relación de potencia, aceite y fricción necesarios para optimizar una operación específica de corte en un maquinado- hasta necesidades más básicas pero igual o más importantes, como enviar una alarma a una persona o sistema para indicar que es necesario vaciar un depósito de basura porque está lleno.
En resumen, pensar primero en escenarios en que todo es posible, y a partir de ahí considerar qué le gustaría medir a la empresa y por qué. Una vez determinada la línea general, habrá que estudiar las opciones disponibles en el mercado para tener una idea de costos y contar con conocimiento de experiencias que podrán seguramente aportar ideas adicionales en la medición y visualización de variables propias.
- Implementación: Obtención, análisis y procesamiento de información
Los datos para obtener indicadores relevantes para la empresa seguramente provendrán de diversas plataformas, máquinas y sistemas. Resulta, por tanto, prioritario pensar en los cuatro procesos necesarios para utilizar la información, que consisten en 1) extraer, 2) almacenar 3) analizar y procesar, 4) e integrar los datos.
Los resultados no van de cero a cien, pues es importante pasar por distintas fases para adaptar las máquinas, procesos y personas a la transformación digital.
La mayoría de las fábricas contarán con dispositivos productivos de distintos niveles de preparación para la transformación digital, que se catalogan de nivel 1.0, 2.0, 3.0 y 4.0, siendo este último el más adaptado para la digitalización e integración de información.
Sobre los procesos, será importante determinar el nivel de porcentaje y digitalización que se pretende llevar a cabo, sentando las etapas para cada una de las fases, y considerando que una integración completa de producción, administración y gestión será posible solo a través de un esfuerzo coordinado entre todas las partes.
Las implementaciones de una fábrica inteligente dependerán en gran medida de las personas: la determinación y claridad de objetivos del equipo directivo, así como de la formación, acompañamiento y conocimiento de los equipos de trabajo que lleven a cabo el proyecto de transformación digital.
Para conocer el verdadero impacto de una automatización y digitalización de una fábrica, se recomienda entonces en la gran mayoría de los casos empezar con una prueba de concepto e implementaciones pequeñas, así como transmitir de manera clara la gestión del cambio y alertar de posibles derivas y/o modificaciones, y una vez probada la tecnología, hacer la transición de manera rápida.
- Tecnologías de Industria 4.0
Entre las tecnologías más importantes de digitalización para obtención de datos y optimización inteligente de los procesos productivos destacan:
El Internet Industrial de las Cosas (IIoT), que refiere a dispositivos interconectados en las fábricas para enviar y procesar datos, con el objetivo de visualizar y monitorear variables de manera rápida. Para hacer posible esta interconexión, se añaden las tecnologías necesarias de extracción de datos (sensores), almacenamiento (cloud computing) y manejo y análisis de esos datos (big data e inteligencia artificial).
Drones, robots autónomos y móviles y robots colaborativos (cobots), que apoyan en ciertas tareas – cargando, desplazando, inspeccionando productos y partes.
Realidad aumentada, que provee a través de dispositivos como lentes información como instrucciones y capas de diseño, evitando por ejemplo la necesidad de buscar y moverse del manual al equipo.
Gemelos digitales, que son copias virtuales de la planta, lo que permite planear y modificar escenarios operativos de forma virtual para analizar los resultados de optimización y una vez validados hacer la implementación física.
Fabricación Aditiva o Impresión 3D, que facilita la producción de pequeñas series y prototipos a la medida, así como fabricar piezas complejas rápidamente y a un costo competitivo.
Entre esta lista se encuentra una mezcla de hardware y software, pues en definitiva se trata de conectar al mundo real con el virtual y viceversa, manteniendo como objetivos claros la optimización de la producción y la reducción considerable de fallos de calidad y seguridad. Existirán, sin embargo, nuevos retos a abordar, entre los que destacan la ciberseguridad, cuya fiabilidad puede jugar un papel fundamental en el éxito o paro total de una producción.
En conclusión, podemos decir que las fábricas inteligentes generan grandes ventajas competitivas por sus resultados en reducción de costos, tiempos y residuos y en la identificación de cuellos de botella y espacios subutilizados de producción, con herramientas que permiten flexibilizar y adaptar de manera rápida el proceso productivo.
Sin embargo, antes de llevar a cabo un proceso de implementación de fábrica inteligente, es necesario hacer un análisis importante de los objetivos, y de la selección de los equipos de trabajo y la tecnología, así como de las decisiones en términos de infraestructura, conectividad y seguridad asociadas.
En primer lugar, se trata de tener identificada, con una visión a largo plazo, una necesidad concreta, que pueda ser estudiada a partir de un ejemplo al que se puedan plantear soluciones tangibles, y a partir de este primer proyecto crecer rápidamente una implementación de fábrica inteligente con un estimado basado en conocimiento previo de tiempos, costos y competencias requeridos.
En definitiva, para una implementación de fábrica inteligente exitosa, como resume Jim Carroll, hay que pensar en grande, iniciar pequeño, y escalar rápidamente.
SOBRE LA AUTORA
Ingrid de Keijser
Licenciada en Ciencias Políticas y Relaciones Internacionales. Máster en Historia de las Relaciones Internacionales y Máster en Periodismo. Sus actividades profesionales se concentran en gestión y comunicación empresarial y corporativa en varios países, con especial hincapié en el sector industrial.
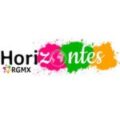